Timberbuilt Solutions Project
Cadwork
- Location
- Montreal
- Manager
- Laurent Decosterd
- Website
- Cadwork
This project in Mount Barker, South Australia, showcases the new possibilities in construction that Timberbuilt Solutions is providing using cadwork 3D teamed with Hundegger precision CNC machines. The free form curved box sections for the main portal structure of the Mount Barker project were modelled in cadwork 3D, in particular the LVL flanges, blocks and stiffener members. Our method of building these curved beams involved “sprung” flanges, which means they were straight LVL components, clamped and sprung into shape for assembly. Some of the beams curved both upwards and downwards in a free form contour. The outer flanges were modelled curved with all cutting and drilling references, then straightened in cadwork. Exporting these straightened objects allowed CNC processing of straight LVL pieces which were then “sprung” into the desired curved shape for assembly, with all drilling, marking and cutting locations correct for the curve.
Sounds complicated? Here is the process flow for a single curved flange:
1) Model the curved flange as a virtual solid object in cadwork 3D with all drillings, markings and angled cuts
2) Take the virtual solid object and straighten it
3) Export this virtual straight object to CNC
4) Process the real straight object in LVL
5) Create the curve with clamps, etc for assembly in curved box section
With cadwork, complex concealed connections can be “virtually built” before manufacture. The cadwork 3D model below shows an internal connection of the plywood box section portal frame.
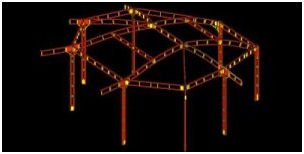
The Wall Frames
By using cadwork 3D, Timberbuilt Solutions can prefabricate buildings with curves, irregular shapes or other unusual elements off-site to high levels of precision. The wall frames of the Mount Barker project were not only curved, but their top plates were also at an incline. To create this type of curved top plate without cadwork 3D would have been almost impossible. The complexity of the wall frames meant that the building client could not obtain a fixed price for the labour, because contractors could not predict how long the walls would take. Timberbuilt solutions were able to give a fixed quotation for the prefabricated walls, manufactured and supplied in individual flat-packed modules which were rapidly and accurately assembled on site in just a few days. Architects, engineers and designers can have the best of both worlds with customized , bespoke structures designed in 3D, supplied prefabricated, then assembled quickly and simply for on-site labour cost savings.
The Roof
Custom trusses were designed and fabricated in LVL and plywood to create the contoured roof structure. All trusses were unique and custom built in Timberbuilt Solutions' factory before being transported to the site . Such a building could not have been constructed with controlled on-site costs without the advanced 3D component modelling with cadwork and computer-aided manufacture with the Hundegger K2. This is true Building Information Modelling (BIM) Complex 3D modelled structural elements are also expressed in 2D working drawings and details for onsite reference.
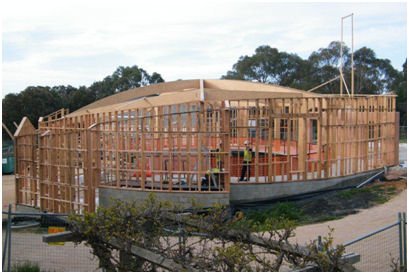
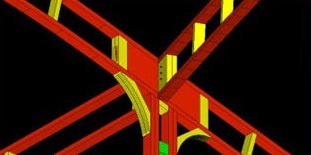
Summary
Timberbuilt Solutions met the challenge of designing a custom structural solution for a unique building, and cadwork 3D was an integral part of the process. Strong environmental outcomes were also achieved with the use of totally plantation grown LVL and plywood products.
By modelling the members and their components in cadwork 3D, Timberbuilt Solutions could produce predictable outcomes in manufacture and performance
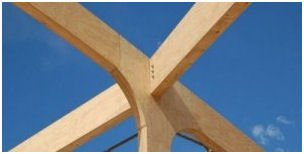
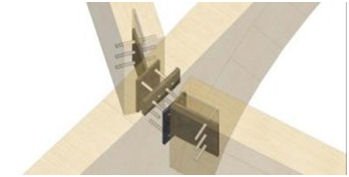
Timberbuilt Solutions Project
Project Information
- Location
- Mount Barker, South Australia